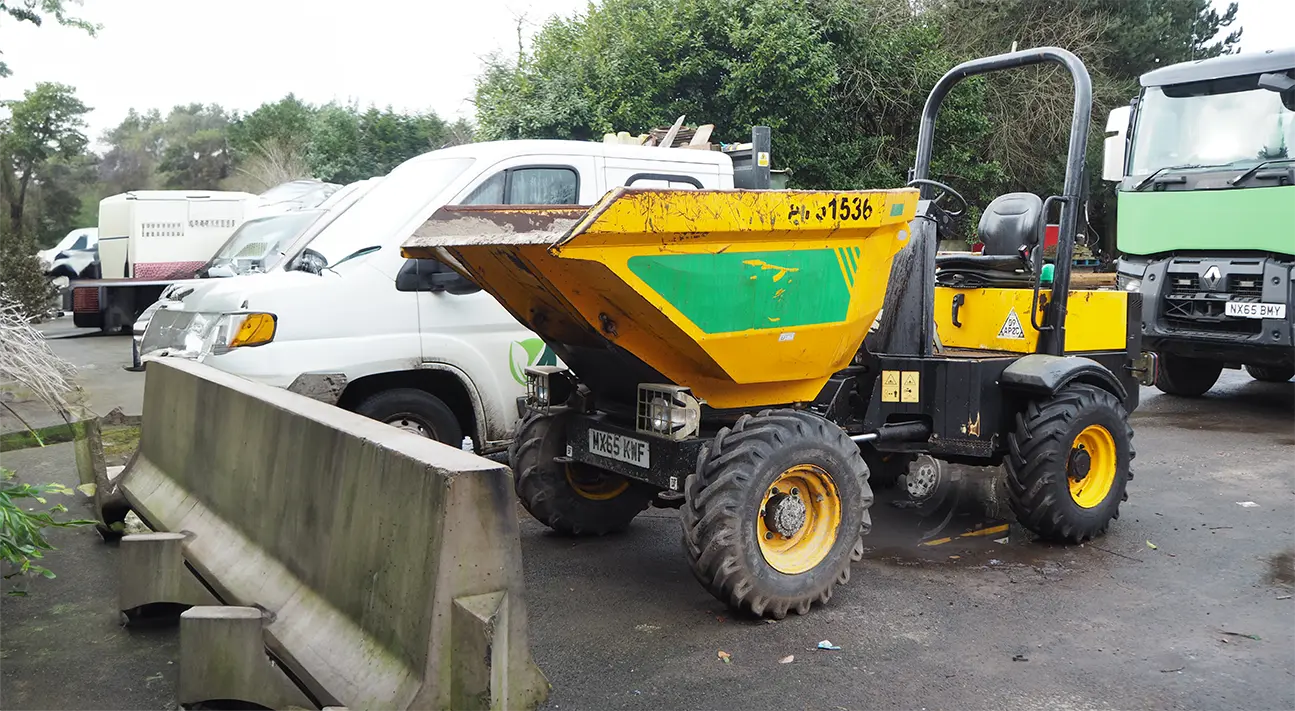
Forward Tipping Dumper Training in Manchester

Fully accredited forward tipping dumper training courses. 1 to 5 day course, depending on experience & number of participants.



Why Pro-Trainers UK?
Trading in Manchester for 15 years
Thousands of satisfied customers
Nationally recognised accreditation
Comprehensive course offering
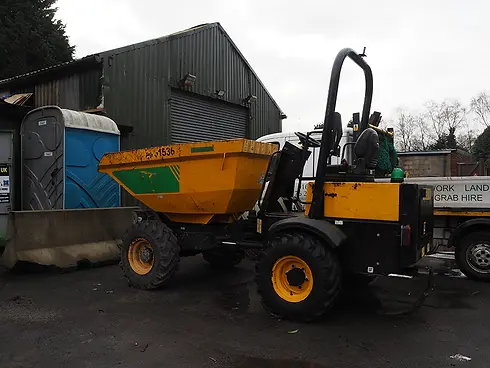
Forward Tipping Dumper training courses
Pro Trainers UK is an accredited plant training organisation in Manchester with the I.T.S.S.A.R. and National Plant (NPORS) training bodies. Our training is delivered to an exceptional standard and is monitored regularly to ensure quality. Our forward tipping dumper certification is nationally recognised and can be used nationwide.
​
Our forward tipping dumper training courses include: ​
-
Certification options for Quality Assurance, NPORS, and ITSSAR
-
Full Certification and Test Fees
-
Provision of ID card with photograph
-
Certificate of Basic Training
-
A detailed course manual with working exercises (except Refresher courses)
-
Forward tipping dumper courses are available onsite and at our training centre.
​
Accreditations
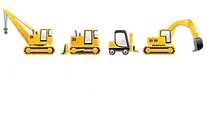

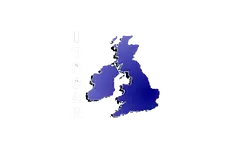
Our Forward Tipping Dumper Training Courses

Forward Tipping Dumper Novice Course
At Pro Trainers UK, we're committed to delivering plant training that not only meets but exceeds the standards set by industry bodies. Our forward-tipping dumper courses are meticulously designed to ensure your team reaches the pinnacle of operational proficiency. We take pride in our detailed assessment reports, tailored specifically to each course, giving you the peace of mind that your employees are fully competent in all aspects of the training.
​
Course Name: Forward tipping dumper training
Target Audience: Novices or operators looking to expand their skills to other types of lifting machinery.
Duration: Varies based on specific needs. Typically 5 days with a maximum of 3 participants
Availability: Our forward tipping dumper courses are available onsite and at our training centre.
Key Learning Outcomes:
-
Acquire the ability to operate a loading shovel.
-
Enhance employability with a broader skill set.
-
Receive a comprehensive certification for forward tipping dumper operation.

Key Assessment Areas
At Pro Trainers UK, we adhere to strict guidelines set by NPORS & ITSSAR to ensure the highest standard of training for your staff. Our detailed assessment reports provide a comprehensive overview of each participant's competency in operating forward, tipping dumpers and instilling confidence in their abilities.
​
Pre-operational Checks: Participants conducted thorough pre-operational checks, ensuring all essential components such as fluid levels, tyres, brakes, and safety devices were in optimal condition. Any deviations or issues were duly noted and addressed before proceeding with operations.
​
Manoeuvring: Trainees demonstrated proficiency in manoeuvring dumpers across the site/training area, both laden and unladen. They navigated varying terrain with precision, adhering to width restrictions and safely negotiating confined areas. Additionally, participants executed hill starts in both forward and reverse directions, showcasing their ability to operate effectively on slopes.
​
Loading and Checks: During loading operations, participants positioned the dumper adjacent to the excavator, ensuring proper alignment and safety. They parked the dumper securely and followed all safety protocols to safeguard against underground services and cables, prioritizing the well-being of other workers on-site.
​
Transportation and Backfilling: Trainees successfully transported loads from excavations and formed spoil heaps on firm, level ground. They effectively transported spoil from the heap and backfilled excavations, utilizing stop blocks and guidance from a banksman where necessary to ensure safe and efficient operations.
​
End of Shift: After the shift, participants parked the dumper safely on firm ground, removed the ignition key, and conducted post-operation checks. They cleaned the skip as required, refuelled the dumper, and meticulously checked for any defects, ensuring the machine was left in a safe and secure condition for the next shift.
Testing and Certification Details

The Practical Test and Its Importance
Our forward-tipping dumper training culminates in a practical test, a crucial step towards certification. This test, validated and approved by either NPORS, ITSSAR or Quality Assurance (depending on your preferences) is a comprehensive evaluation of your crane operating skills. Passing this test signifies that you have attained the proficiency required to operate a dumper safely and effectively. It's important to note that this test is not just a formality; it's a rigorous assessment that ensures you are ready for real-world plant operations.
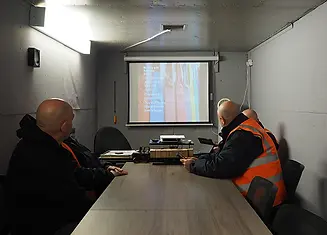
Three stages of Training
Basic Training: This is where you'll learn the fundamentals of plant operation, including handling and safety procedures. It's the first step towards becoming a competent operator.
Specific Job Training: Tailored to your workplace, this stage includes training on specific handling attachments and knowledge of the work environment.
Familiarisation Training: Conducted on the job under close supervision, this stage allows you to apply what you've learned in a practical setting, ensuring you're comfortable and competent in your specific work context.
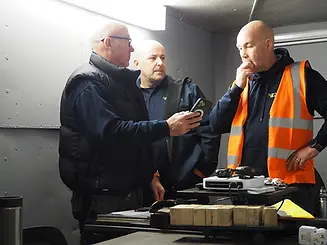
Test Revisions & Expectations
The practical test has undergone revisions to ensure it remains relevant and challenging. These changes include an updated marking sheet, where certain faults may now score higher, reflecting the emphasis on safety and precision in operations. Additionally, the test now includes a written component, where candidates are expected to achieve a minimum score of 80%. This includes both multiple-choice and open questions, ensuring a comprehensive understanding of both practical and theoretical aspects of dumper operation.
FAQ's
What is the duration of the forward tipping dumper training course?
Our forward tipping dumper training courses typically last one to five days, depending on the level of experience and the specific needs of the participants.
​
Are there any prerequisites for enrolling in the course?
There are no formal prerequisites for the forward tipping dumper course. However, participants should have a basic understanding of construction site safety and machinery operation.
​
Can the training be conducted onsite at our location?
Yes, we offer onsite training at your location for convenience and practical relevance to your work environment. Alternatively, participants can also attend training sessions at our designated training centres.
​
Who conducts the training sessions?
Our training sessions are conducted by experienced and certified instructors who adhere to the guidelines set by NPORS & ITSSAR, ensuring the highest standard of training delivery.
What topics are covered during the training course?
The training course covers a wide range of topics, including pre-operational checks, safe manoeuvring techniques, loading and transportation procedures, site safety protocols, and end-of-shift procedures.
​
Is certification provided upon completion of the course?
Yes, participants who successfully complete the forward tipping dumper training course will receive a certification accredited by NPORS & ITSSAR, validating their competency in operating forward tipping dumpers.
Can the training be customised to suit our specific work requirements?
Absolutely, our training programs can be tailored to address the specific needs and challenges of your work environment, ensuring maximum relevance and effectiveness for your team.
​
How many participants can enroll in each training session?
The maximum number of participants per session depends on the level of experience and the specific training requirements. Generally, we recommend smaller class sizes to optimize learning and practical experience.
​
What safety measures are in place during the training sessions?
​
Safety is our top priority, and our training sessions are conducted in accordance with industry safety standards. We provide comprehensive safety briefings, personal protective equipment (PPE), and practical demonstrations to ensure a safe learning environment for all participants.
​
How can I book a forward tipping dumper training course for my team?
To book a training course or inquire further about our forward tipping dumper training offerings, please contact our team at Pro Trainers UK. We'll be happy to assist you in scheduling a session that meets your needs and objectives.
Testimonials

Our Team.
Welcome to the heart of Pro Trainers UK, where our strength lies in the expertise and dedication of our team. Behind every successful training course is a group of passionate professionals committed to providing the highest standard of heavy machinery training.
Our Plant Training Courses
Find our Training Centre in Manchester
Our operating Areas include Altrincham, Ardwick, Ashton under Lyne, Blackfriars, Bramhall, Broughton, Bury, Cheetham Hill, Chorlton cum Hardy, Collyhurst, Denton, Didsbury, Droylsden, Dukinfield, Eccles, Failsworth, Gatley, Heaton Moor, Hulme Hall, Hyde, Irlam, Longford, Manchester, Marple, Middleton, Moss Side, Oldham, Partington, Pendleton, Prestwich, Radcliffe, Ringway, Rusholme, Sale, Stalybridge, Stepping Hill, Stockport, Stretford, Swinton, Trafford, Urmston, Walkden, Whitefield, Woodley, Wythenshawe.